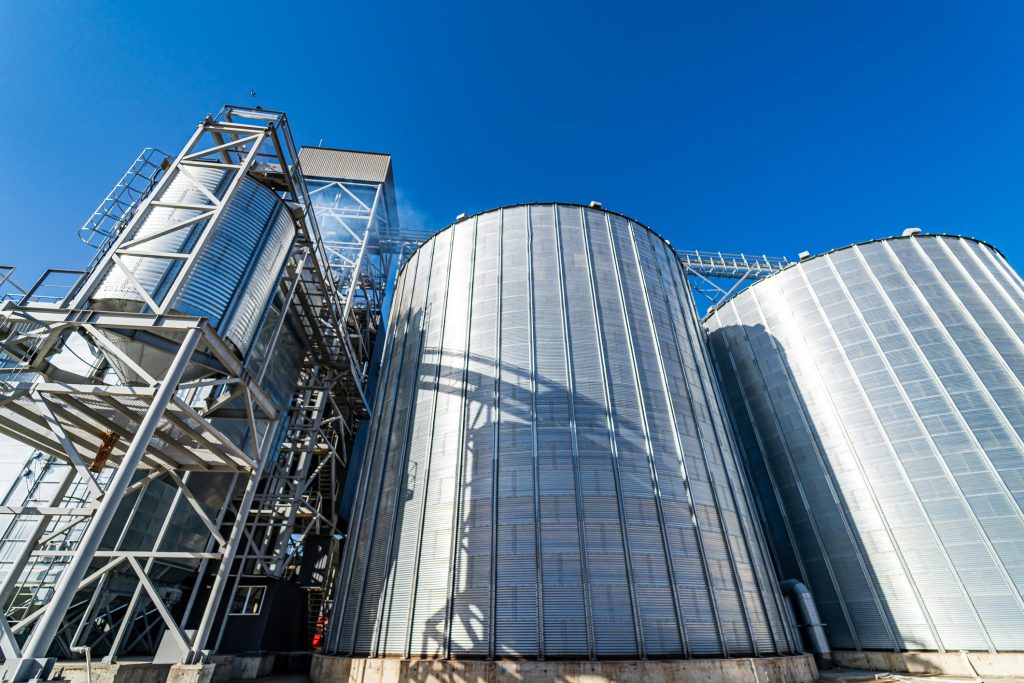
With proper planning and the right equipment, a feed mill can operate seamlessly with minimal supervision or oversight required. There are multiple ways to improve feed mill efficiency. This includes improving production speed, reducing maintenance costs, reducing downtime, reducing error and waste, improving safety, and more.
6 Ways to Improve Feed Mill Efficiency
1. Bulk Bag Ingredients and Unloading
Bulk bags have the potential to improve feed mill efficiency in a variety of ways. While major ingredients, such as corn and other grains, benefit from the cost savings and quick filling of bulk ingredient storage and dispensation, minor and micro ingredients often don’t.
Replacing 50lb bags with bulk bags or super sacks can make unloading more efficient, reduce employee injuries from repetitive stress, and provide cost-savings that come from buying in bulk. Making this improvement is easy, too. You’ll need to find a reliable supplier who ships your ingredients in bulk, which your current supplier might already provide. You’ll also need a bulk bag or super sack unloader that is sturdy and reliable. With a few bulk bag unloader design optimization tips, you can ensure that material flows through the bag smoothly without the need for supervision.
2. Automated Downstream Routing
Making sure that material finds its way to the proper bin during loading may be as simple as pressing a button, but it can be even simpler than that. Automating the downstream routing process ensures that material moves into the next bin the moment that the previous bin is filled. This means there’s no delay if an employee moves away from the routing mechanism to deal with another machine or task.
To accomplish this, you’ll need sensors integrated with the control system. Position sensors or level indicators will tell the system when to change the position of the turnhead and move material to the new bin.
3. Microingredient Automation
Microingredients can present many challenges. This step in the process also presents an opportunity to improve feed mill efficiency.
It’s important for microingredent systems to be accurate as well as fast. Automating this process allows minor ingredients or microingredients to be added in a similar manner to macroingredients. The system will feed, weigh and dispense microingredients into the mixer instead of hand-adding them using a pre-weighed scoop. This means employees are free to take on more important tasks, and it removes the potential for human error that can result in adding too many scoops or forgetting a scoop.
4. Coordinating Mixing and Filling Times
When the mixer and scales work in perfect harmony, there’s no idle time. This maximizes the machines’ productivity and improves the feed mill’s efficiency. To coordinate these processes, you’ll need to consider how long it takes each process to cycle, fill, settle, weigh, and discharge.
Measure how long it takes all ingredients to fill, settle, weigh and then discharge into the mixer. Then, consider how long the mixer requires to adequately mix the ingredients. If the mixer is sitting idle while the scales are still filling, consider how you might speed up this process by adding a scale or speeding up the filling process. Or, if the scales are waiting for the mixer to finish, you can speed up this process by adding a mixer or changing the mixer or agitator profile.
5. Monitoring Equipment
When sensors work with your control system, you can prevent damage, hazards, reduce maintenance needs, and plan downtime. There are many ways to monitor your equipment. Monitoring the vibration or temperature of the bearings on a grinder or conveyor, for example, can help to prevent uneven wear. These sensors can also show if a pebble or another object is damaging the machine. Monitoring the temperature of the bearings can prevent damage due to overheating from friction. This can also be a source of sparks, which can cause a fire or explosion in environments with excessive dust, like a grain elevator shaft.
6. Reducing Damage
When a machine is damaged during production, it can shut down the entire facility and cause expensive downtime. Preventative maintenance is essential to prevent these situations. Keeping bearings lubricated on all machines, keeping the seals maintained on mixers, checking the tensioning on drive belts and chains, cleaning intervents, and checking electrical components on a regular, well-defined schedule will extend the lifetime of your machines, and reduce the need for costly repairs.
Use these upgrades to improve feed mill efficiency and safety. With the right planning, you can make your machines work seamlessly and create a workplace that is both safe and highly productive.