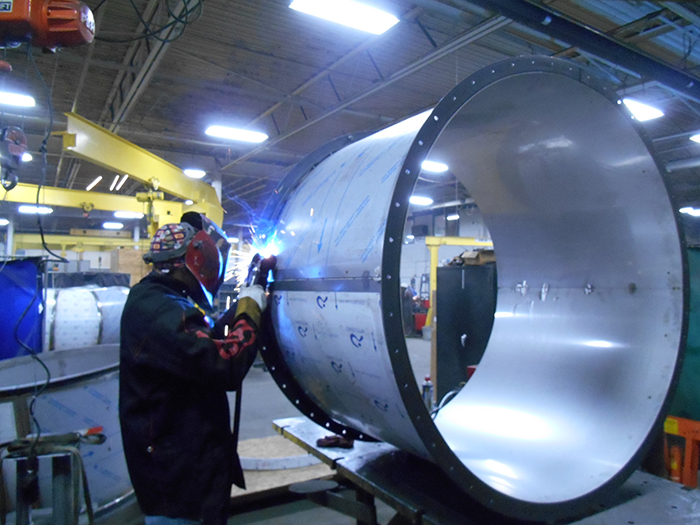
Sheet metal rollers are essential for custom fabrication machine shops for a wide variety of applications and industries. The rollers can create arcs, bends, cylinders and circular objects. With the correct type of sheet metal rolling machine, you can improve product quality, system efficiency and process reliability.
This guide examines the various types of sheet metal roller machines and their applications in industrial settings for custom fabrication.
What Are Sheet Metal Rolling Machines?
Sheet metal rollers, also known as plate rollers or roll-bending machines, are used to bend steel into curved, cylindrical, or conical forms. The sheet metal rolling machines use rollers to curve the sheet metal as it passes through the machine. It controls the diameter, curvature, and shape.
These types of machines are commonly found in fabrication shops, metalworking facilities, and manufacturing plants that work with steel, aluminum, stainless steel, and other metals.
From food manufacturing to pet food and chemical applications, metal rollers are a key part of APEC’s customized system solutions, like conveyors, coaters, feeders, and more.
Three Types of Sheet Metal Rollers
Two-Roll Machine
The 2-roll sheet metal rollers involve two rollers: the larger one is coated in urethane, and the other one applies pressure to the sheet metal to create the arc or curve.
Applications:
- Rolling lightweight metal sheets
- Craft or custom metalwork
- Entry-level bending operations
Three-Roll Machine
Three-roll machines are widely used in the metalworking industry. The third roller provides more control over the final shape, allowing it to be used for tighter cylinders. When the sheet metal leaves the roller, it can then be welded into a completed cylinder shape. The two designs include:
This sheet roll machine is best for high-precision rolling and more consistent results.
Four-Roll Machine
Four-roll machines offer maximum control and automation. The sheet is fully clamped and guided through all four rollers, allowing for both pre-bending and continuous rolling in one pass.
This sheet metal roller can also make square- and rectangular-shaped objects. The machines tend to be faster, more accurate and are capable of working with much larger objects and much thicker metals.
Applications:
- Industrial-scale fabrication
- High-volume rolling operations
- Producing tubes, tanks, or shells with tight tolerances
Choosing the Right Sheet Metal Roller
When choosing the right roller for your application, consider these factors:
- Material type and thickness
- Bend radius requirements
- Production volume and repeatability
- Automation and CNC compatibility
Choose APEC
If your custom fabrication project requires cylindrical or conical constructions, it is important to choose the right sheet metal roller. With the right equipment, your custom fabricator can construct components more quickly and inexpensively.
Looking for a custom solution for your project? Reach out to APEC today!