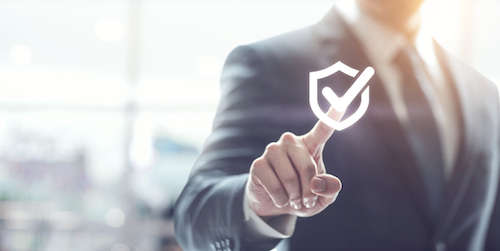
In our previous post, we discussed the benefits automation equipment can have on business and on workers. One of the benefits of automation equipment and robots over humans is the machines’ ability to perform the same task continuously, consistently and reliably, without risk of injury and little risk of variation. However, this can only work if the machine is installed and programmed correctly, and regularly maintained. To optimize automation performance, it’s important to keep in mind a simple, but powerful maxim; “Trust, But Verify.”
“Trust, But Verify”
“Trust, But Verify” is a Russian proverb that first made its way into popular English during the Cold War and nuclear missile disarmament. It’s now used in many contexts, including automation. “Trust, But Verify” essentially looks at the process and the result; trust that the process works correctly, but verify that the result is correct.
This is especially important for optimizing automation performance, and ensuring that the process is working. While a person may perform an error a few times and then fix it themself, a machine will continue to perform the process incorrectly until the source of the problem is fixed. This means, without verification, a process may be incorrect for long periods of time. These errors can also multiply across the production line, turning a small problem into a dangerous product defect.
Process Verification in Manufacturing: Then and Now
Previously, a battery of tests was the best way to determine whether a process was running properly. Usually, this involved taking a sample and delivering it to a lab. The lab might test for values such as PH, humidity, temperature, fat content, protein content, sugar brix content, water content, weight, product hardness, elasticity, and manufacturing defects that might affect the visual appearance or the structural integrity of the product. This verification process was slow, with many potential pitfalls.
Now, many of these factors can be tested in real time on the factory floor, often with sensors or spot tests. There’s no need to halt the process while waiting for lab results, or recall product that turned out to test badly. However, this also means that a faulty sensor can cause product defects and incorrect processes to go unnoticed. Though it’s reasonable to trust that a quality sensor works, it’s necessary to verify this as well.
These process verification procedures can help to ensure that the information you’re receiving from sensors is accurate, and that automated machines are performing the process properly.
6 Verification Procedures to Optimize Automated Equipment
1. Calibration
Sensors, weighing instruments and other equipment must be regularly calibrated to maintain accuracy. This is one of the most important verification procedures to optimize automated equipment, and should not be left to chance. Otherwise, the machine’s accuracy is left to chance as well. Establish a clear calibration procedure for each instrument using the manufacturer’s instructions. Make sure workers know who should carry this procedure out, and when.
2. Redundancy
For procedures that must be very precise, or for processes that are prone to error, you can optimize automated equipment by using redundant sensors. While one sensor may fail, it’s unlikely that two would fail at the same time. Using two sensors can also help you see if one has become inaccurate.
3. Reduce Interference
Where possible, use instruments that are digitized locally to the sensor. Electromagnetic interference, vibration, or damage to wires can cause signal transmission errors across longer distances. If you’re transmitting analog values, be sure that you have a secure ground reference, and that the signal is properly spanned.
4. Use Reference Values
Reference values give you a baseline for what is accurate and correct. Without reference values, it’s difficult to know when your sensors and machines are working properly. Use test weights, optical references, voltage outputs and other measures to verify that the process is working properly.
5. Regular Maintenance
Regular maintenance is an essential process verification step to optimize automated equipment. The machines as well as the sensors should both be regularly maintained according to manufacturer’s recommendations. This includes cleaning procedures to prevent the build-up of dust and debris, visual inspections of wires and faceplates, replacing seals where necessary, and more. Some measurement devices, like hermetically sealed load cells, generally do not need maintenance as frequently as other, unsealed devices.
6. Visual Inspections
Establish visual standards and inspections so workers can spot a problem if it occurs. This might include visually inspecting the finished product, or inspecting the product as it moves through the process. Consider the product’s color, size, consistency, or other notable features. Be sure there is a procedure in place for reporting and fixing a problem if a worker detects it.
“Trust, But Verify” works on a fairly simple principle; you need to trust that your process works, but also make sure that it does. Using process verification procedures will not only help you optimize automated equipment, but also prevent problems, reduce costs and give you peace of mind.