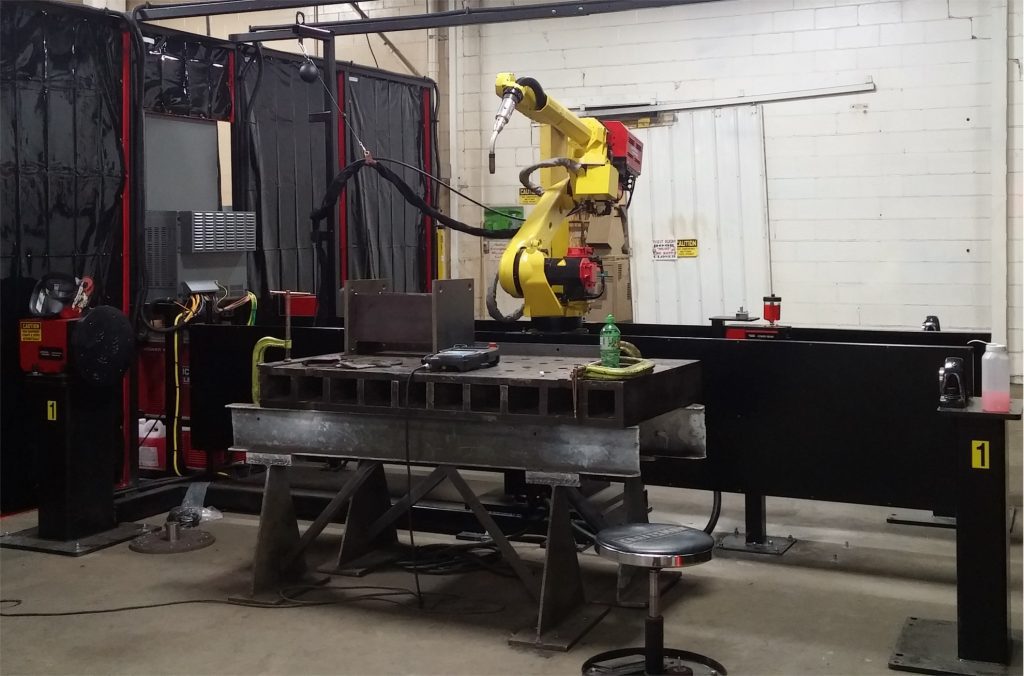
Automation can improve the efficiency, safety, accuracy and speed of a process, but it also requires careful planning. There are many factors to consider and it can be difficult to know when a process should be automated. If you are wondering about automating a process at your food processing plant, manufacturing plant, or another facility, consider the following.
How to Know When a Process Should be Automated
1. Current Process Time vs. Projected Process Time
Time is one of the most important factors to consider when deciding whether a process should be automated or not. A machine will perform most simple and repetitive processes faster than a person can. However, it is not only the individual process itself that should be considered, but the surrounding processes as well.
For example, when comparing an automated weighing and batching system to a manual system, it is important to consider the time it takes a person to open and transfer materials, as well as weighing and batching the materials. Automating this process may mean using bulk bags, which will reduce the time needed to open and dispense bags. Conversely, if a process takes only a moment for a person to perform, automation may not provide much in the way of time-savings, unless multiple processes can be automated at once.
2. Accuracy Requirements
Accuracy is another important factor to consider when a process should be automated. If machines are installed, maintained and programmed correctly, they will perform the same task, the same way, within a set margin of error, each time. A person, on the other hand, may be tired or distracted, and push a button or lever twice, add in too much or too little of an ingredient, or perform a process in the wrong order. Automating a process can increase product quality, decrease material waste, and reduce liability from potentially dangerous defects.
3. Process Complexity
In the last decade, automated machines, robots and computer programs have become increasingly advanced. Powered by the right AI, a machine can perform very complex tasks and even apply a version of critical thinking. However, these machines are also expensive. For this reason, process complexity is important when considering whether a process should be automated or not. Simple, repetitive tasks will be most effective and most economical to automate. Conversely, monitoring processes, inspecting finished products, performing maintenance, and other, more complex tasks, are best performed by people.
4. Safety and Hazards
Some processes introduce humans to dangers and health hazards. These processes are ideal to automate. Eliminating stress injuries due to repetition are among the most common benefits of automation. Processes involving dust, toxic chemicals, or fumes should also be considered for automation. While machine parts can be reinforced and shielded from caustic chemicals, it is much harder to adequately protect a person, especially over a long period of exposure. This is why many cleaning, painting, and coating processes are among the first candidates for automation.
5. Material Stability
Some materials are relatively predictable and easy to handle, while others are more chaotic and difficult. A sheet of steel, for example, will move through a process in a very predictable manner. A machine can easily handle these materials and move them along an assembly line. Powders, on the other hand, are more sensitive to outside forces like changes in temperature or humidity. Even slight changes can make them behave in unpredictable ways. Processes working with powders and other difficult materials can still be automated, but these machines may require additional supervision and more careful planning.
6. Labor Costs vs Automation Costs
This is the most common consideration when determining whether a process should be automated or not. When comparing automation and labor, it is important to take all costs into account. Automating a process not only eliminates direct labor costs such as wages and overtime, but it can also reduce indirect costs such as those from work injuries, worker’s compensation, liability, paid leave, overtime, retirement benefits and more. From the automation standpoint, consider costs of maintenance and installation, as well as the equipment itself.
7. Future Growth
Consider your markets, and gauge your expected future growth or contraction. Machines can work much faster than people, and can help you keep up with increased demand and continue growing. However, if you expect a decline in demand in the near future, this added speed and productivity may not be worth the investment at this time.
There are many factors impacting whether a process should be automated or not. In some cases, it is easy to automate a process that is otherwise long, arduous or unsafe. In other cases, it can be a more difficult decision. It can be helpful to make a list of estimated costs and time-savings, safety considerations, advantages and disadvantages when making this decision. Compare these items, and you can be confident in your decision to automate or leave the process the same.