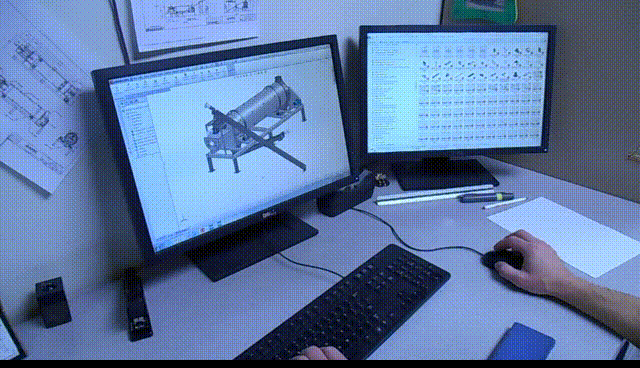
CNC machining includes a wide variety of machine and machining techniques, which can produce many different types of products. From complex product prototypes to high-volume manufacturing runs and everything in between, CNC machining helps to fill in production needs, develop new products, design solutions, and more. With the right tips, you can reduce costs on your CNC machine job and make your overall project more cost-effective.
Tips to Reduce Costs on Your CNC Machine Job
1. Perfect Your Design
Whether you have a simple and straightforward design or a complex blueprint for a prototype, one of the best ways to reduce costs on your CNC machine job is to complete and perfect your design. When your design is clear from the start, the machine shop you work with will not have to spend time and resources making edits or changes. A clear and readable design will also help to prevent defects or misunderstandings that could extend your timeline and add unnecessary costs.
If you have already used your designs at your own machine shop and you are seeking a manufacturing partner to fulfill demand, it may still be a good idea to assess your files. What is clear for your shop and your staff might not be clear to another.
If you’re not sure how to perfect the design of your project, here’s a few questions you can ask a machine shop to find out.
- File types: ask what file types are ideal for the machine shop, and create these files, if you can.
- Weld specifications: the machine shop may need details about weld specifications, and can provide some guidance if you’re not sure what these would be for your project.
- Changes: ask if there are any changes you could make to your design to make your project simpler or more affordable. Sometimes, small changes can substantially reduce costs.
- Machines: ask what machines the machine shop will use to complete the project. Also, ask if there are alternative machines that could make the project simpler, or if the machine shop anticipates any challenges to completing your project.
- Questions: ask the machine shop if there are any aspects of your design that are unclear or if they have any questions, so you can clear them up right away.
Learn more about the benefits of custom fabrication and what to expect
Download The Metal Fabrication Subcontracting Decision Guide
2. Choose the Optimal Process and Machine
There are many ways to complete a CNC machine job. Sometimes, a relatively simple machine can complete a job with speed, accuracy and efficiency. Other times, a more sophisticated machine can complete the job much faster or more cost-effectively.
If you already have experience with your own or another machine shop, you may already have a machine in mind that can do the job. If not, or if the project is unfamiliar to you, it may be more difficult to know what type of machine is ideal for your project. Asking different machine shops the right questions can help you narrow it down. Also, understanding the functions of different CNC machines, such as laser welders, lathes, mills, rollers, and other machines can help point you in the right direction.
So, what questions can you ask to help find the right machine and reduce costs on your CNC machine job?
- Example products: Ask about the ideal or most common products each machine produces. This will give you a better idea of each machine’s optimal functions and whether or not the machines available are right for your project.
- Sizes: Every machine has some limitations on the size of the objects it can work with. Ask about size limitations on each machine if it isn’t clear. This way, you can make sure you get the right fit.
- Speed: Ask how fast each machine works, and the average rate for each machine. If you have a variety of small pieces or a number of repetitive moves required, you can get a baseline price for each. This will also help you compare rates for different shops and help you see which machine shop has the best equipment for the job.
- Differences: If two different machines seem to be appropriate for a particular aspect of your project, ask about the differences between each. For example, a lathe and a mill are similar machines, but each has optimal jobs. Understanding the differences can help you find the right machine.
3. Use the Right Materials
The right materials can make a big difference in the overall price of your project. This may seem obvious, but it’s important to consider multiple aspects of your materials. For example, a material may seem more affordable at first, but if it causes the product to rust or fall apart prematurely, it won’t be more affordable in the long run. Finding the right balance between durability and affordability can help you reduce costs on your CNC machine job.
Depending on your project, you may want to consider different metal alloys or plastics. Consider how you need your product to perform and make a list of the following factors to find the ideal material for your project.
- Flexibility: Some materials are easier to machine than others. Consider this as you decide what materials to use.
- Temperature: Some metals or plastics will melt, warp or freeze at extreme temperatures, or with excessive friction.
- Corrosion resistance: If your product will be exposed to weather, salts, acids, or alkalis, you’ll need to consider corrosion resistance.
- Weight: Some materials are less durable, but lighter, which can be a notable advantage for some projects.
- Cost: Cost, of course, is an important consideration. Finding substitutes can help you avoid demand spikes or work around material shortages.
Asking the right questions can help you reduce costs on your CNC machine job. Talk with different machine shops and experts to learn which designs, machines, and materials are ideal for your project. To learn more about the machines and functions available at APEC, take a look at our custom fabrication guide.