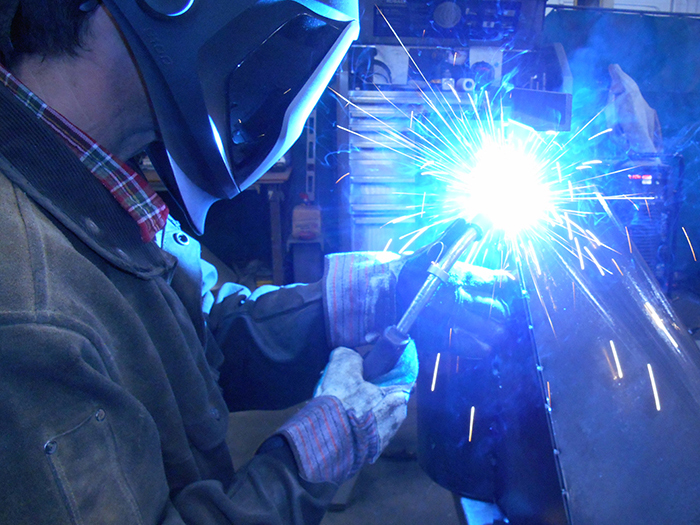
Welding is one of the most important processes in manufacturing. From prototypes to rapid production of small metal parts to fabrication of large metal machines, welding helps to keep all the pieces together. There are many different types of welding and different welding techniques. Robot welding uses robotic assistance and automation, while manual welding relies on human ingenuity and expertise. Let’s take a closer look at manual welding vs robot welding, and see which might be best for your fabrication project.
The Differences Between Manual Welding & Robot Welding
What is Robot Welding?
Robot welding may refer to completely automated welding processes (usually spot welding), or it may refer to robot-assisted welding. Robot welding has helped to make many manufacturing and fabrication processes safer, as the robots can move human operators further away from dangerous or monotonous tasks. As technology has progressed, robot welding has become more sophisticated and more efficient. A robot can be programmed and designed to perform many different types of welds, including arc, resistance, spot, TIG, MIG and more. However, it is still no substitute for manual welding from an experienced welding.
A robot welding machine might be programmed to perform a particular weld over and over again, such as in an assembly line. Or, a robot welding machine may work alongside a person; a person prepares the materials and the robot performs the weld. Finally, a robot might assist a person and work under an operator’s instructions to perform tasks that an unassisted person might not be able to perform otherwise.
Learn more about APEC’s welding and custom fabrication services
Download the Custom Fabrication Guide
What is Manual Welding?
Manual welding is performed by a person, using many different types of welding machines. With the right experience, a welder can perform many different types of welds, including arc, resistance, spot, TIG, MIG and more. Someone may become a welder by completing an apprenticeship program at a business or completing a formal training program. Welders may gain a certification through the American Welding Society to show that they can perform particular welding operations and work with different types of materials or in different industries.
Manual welding technology has also advanced alongside robotic welding technology. This technology has allowed welders to make more complex welds, use different techniques, use different materials, and weld safely and more efficiently. In some cases, the line between manual welding and robotic welding can become blurry, as a welder might use robotic assistive technology to improve their speed or technique, or get distance from a dangerous job.
Benefits of Robot Welding
There are a number of benefits to robot welding. Though robots can sustain damage, they can also be repaired, and their injuries are much less serious than those a human would endure in welding. This makes robot welders ideal for dangerous jobs that might over-exert a person. Robots are also ideal for performing repetitive, monotonous tasks. The robot can be programmed and set up one time and perform the task over and over again without the need for much supervision. A person is more likely to become fatigued by this job and make mistakes or even suffer injuries.
Benefits of Manual Welding
Manual welding also has many benefits. Though human welders might not be as exact or as tireless as robots, they have the ability to perform more complex tasks without the detailed programming or technology that a robot would need. For detailed work or complex welds, especially those that are not in straight lines or at right angles, a person is likely to complete these welds better. A person should also supervise robots, even those that are completing monotonous tasks. If a robot is damaged or isn’t calibrated or programmed correctly, it could potentially perform the task incorrectly numerous times and create multiple defects before it’s noticed. A human supervisor will notice this and, with the right tools and training, will be able to fix it.
Both manual welding and robotic welding have advantages and disadvantages. These types of welds can be ideal in different situations. If you are fabricating large or complex products or machines, or you require especially detailed welds for food-grade machinery, manual welding may be the best choice. If you are working with numerous, smaller parts and large runs, robotic welding may be best.
Choose the Right Welding Method for Your Project
APEC’s experienced welders and robotic welding machines have fulfilled many different custom fabrication jobs. If you have questions about manual or robotic welding, or other fabrication processes, contact us.