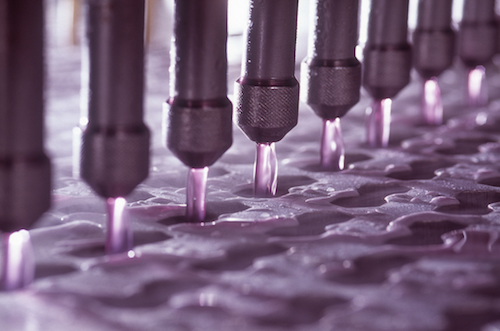
Pumps are one of the most valuable and integral parts of a liquid system. Whether you are working with liquid systems in food processing, pharmaceutical products, chemicals, or something else, it’s important to get the right pump. Choosing the right pump for your liquid system design depends on the characteristics of the fluid, as well as metering, volume, continuous flow or pulsation, and other factors. Let’s take a closer look at the most common types of liquid system pumps.
How to Choose Liquid System Pumps: Comparing the Most Common Liquid Pumps
Centrifugal Pump
Centrifugal pumps use an impeller to generate centrifugal force and move liquids. These pumps are some of the most commonly-used across a wide variety of industries. However, when it comes to liquid systems in food processing, centrifugal pumps can run into challenges. These liquid system pumps are ideal for liquids with relatively low viscosity, such as water and light oils. Centrifugal pumps are also ideal for steady flow applications. Slippage or cavitation can occur when conditions change, so centrifugal pumps are not ideal when metering is required.
Diaphragm Pump
A diaphragm pump is a type of positive displacement pump which uses a flexible, reciprocating layer of plastic or rubber to change the volume of a chamber and force liquid through. While a centrifugal pump is designed to work continuously, a diaphragm pump uses a pulsing motion. This makes it ideal for metering liquids. Diaphragm pumps can also work with thick, viscous liquids and suspensions with abrasive solids. The pump drive can be pneumatic or electric, so it can be used in liquid systems installed in challenging environments as well.
Gear Pump
A gear pump uses the intermeshing teeth of gears to move liquids. These pumps are repeatable and capable of generating high pressures, so they’re suitable for many different applications. However, suspended or abrasive solids can wear down the gear teeth, so these pumps work best with liquids with high lubricity, like fats and oils. These liquid system pumps should not run dry, so it’s a good idea to use a sensor on the supply tank to shut off the pump when liquid isn’t present.
Sinusoidal and Progressive Cavity Pumps
Sinusoidal pumps use a wave-shaped rotor to create moving chambers and move liquid through. This pump is gentle and predictable, making it ideal for thick suspensions in food processing, such as pie fillings, jams and salad dressings. Though these pumps are more expensive than the previous models, they are also easy to maintain and highly effective for challenging, viscous liquids.
Progressive cavity pumps are similar to sinusoidal pumps in many ways. Progressive cavity pumps use a corkscrew-like rotor inside of a flexible sleeve to create moving chambers and move liquid. This pump also generates low shear and gentle force, so it works well with thick liquid suspensions.
Peristaltic Pump
A peristaltic pump uses a flexible hose and an outside rotor to move liquid through. This type of pump is most commonly used in medical applications; you’ll see this pump at work in heart-lung machines and hemodialysis machines. A peristaltic pump is ideal for medical applications because the liquid is completely enclosed. The rotor moves over the flexible tube, but never contacts the liquid, so there is no chance of contamination. For this reason, peristaltic pumps are often used in liquid systems producing pharmaceutical and medical products. They can also be used for caustic chemicals which can be contained by flexible plastics, but can react with other parts of the machine.
Peristaltic pumps operate with tight tolerances and very repeatable flow rates, so they’re ideal for metering exact amounts. The repeated pinching and flexing of the hose will cause it to wear out over time, so a regular maintenance and replacement schedule will be important when working with this type of pump.
General knowledge of the most common types of liquid system pumps will give you a better idea of what you’re looking for, and risks to look out for. As you compare liquid systems pumps, consider the characteristics of the liquid that you’re working with, as well as how you are metering liquids, and the surrounding environment. With the right type of pump, you can minimize maintenance, waste and downtime, increase accuracy, and install a high-performing, long-lasting liquid system.