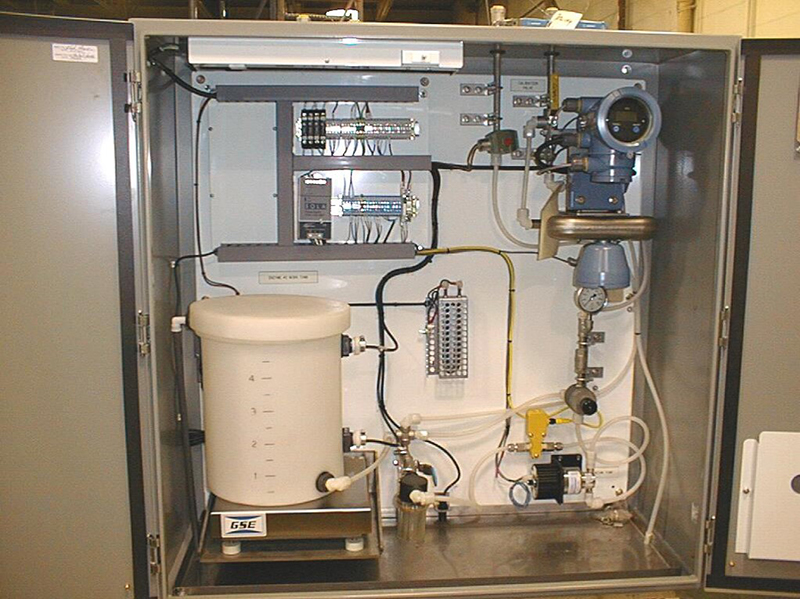
Liquid dosing systems are used in a wide variety of industries in applications, from food and beverage to pet food, industrial chemicals, pesticides, sanitation, and many more. To design the right liquid dosing systems for your needs, it’s helpful to understand the basic components of the system and how the liquids you’re working with interact with them. The basic components of a liquid system are the storage vessel, pump, liquid measurement device, environmental sensors and controls. Though there are exceptions and unique specifications for many different systems, the following are general guidelines to keep in mind when it comes to designing your liquid dosing system.
Designing Liquid Dosing Systems
Know Your Liquid Characteristics
Having a good understanding and an accurate record of liquid characteristics will help you design the best liquid dosing system. The supplier of the liquid should be able to supply this. Consider best practices for storing and handling the liquid, as well as how well it flows, what it reacts with, and more. Start with the following liquid characteristics:
- pH
- Viscosity
- Specific gravity
- Preferred process temperature
- Water soluble
- Oil soluble
- Solution vs suspension
- Reaction to agitation
- Chemical interactions
- Corrosiveness
Storage Vessels
The characteristics of the liquids, as well as the amount of liquid you’re working with will both determine how to design the storage vessel in your liquid dosing system. Safety is an important consideration to start with. If the liquid is flammable, it must be stored in a protective container that prevents combustion during storage and transport. Strong acids or bases must be stored in vessels that prevent corrosion. For food grade applications, the contact surfaces must be easy to clean and sanitize. Some chemicals, such as cyanoacrylate, are very sensitive to moisture, so the vessel must be securely sealed. When working with toxic or hazardous materials, a secondary spill containment unit will be necessary.
For the size of the storage vessel, carefully record the delivery method and the liquid use rate. In some cases, it may be possible to use the liquid directly from the container it’s shipped in. Some systems can unload drums and liquid IBC’s with no need for interim storage. When using these systems, it’s ideal to stage a container with the necessary hookup and valve assemblies. This way, the flow of the liquid is not interrupted when a container is empty. When drawing liquid from these containers, use a pump with high suction at the inlet, and slightly tilt the vessel towards the discharge opening to fully use the product.
Pumps
Choosing the right pump plays a vital role in designing liquid dosing systems. Once again, pay close attention to the material characteristics here. Consider reactions the liquid might have with metals, erosive damage that might occur from suspended solids, as well as the liquid’s viscosity and how hard the pump has to work.
If the application calls for a simple transfer of liquid without a great deal of back pressure, then a centrifugal pump may work fine. To keep the pump working at higher pressure, you can add stages to the centrifugal pump. Centrifugal pumps can suffer some slippage or cavitation if conditions change, so they are usually not a good choice for metering.
For metered liquids, positive displacement pumps are a better choice. There are many different types of positive displacement pumps, including diaphragm pumps, gear pumps, lobe pumps, sine pumps, progressive cavity, peristaltic and piston pumps. For thicker liquids or suspensions, a diaphragm pump may be ideal. Gear pumps are highly repeatable and can generate high pressure. These types of pumps are ideal for liquids with high lubricity, like fats and oils, but they do not work well with suspended solids. For thicker liquids containing suspended solids, such as fillings, jams and dressings, a sine pump or progressive cavity pump is generally a good choice.
Regardless of the type of pump used when designing your liquid dosing system, it’s a good idea to monitor the temperature and pressure of the liquid to make sure that it is within the process tolerance. A little bit of monitoring can save having to replace a costly pump later on.
Meters
The right meter will ensure the right amount of liquid is being used. Most liquid system meters are either volumetric or mass flow devices. Volumetric devices operate by displacing a known volume, usually working with a nutation disk or piston. The meter monitors the number of rotations and translates the number into a flow rate. These types of meters are ideal for liquids that won’t change in density and don’t require a high level of accuracy.
A mag meter uses velocity to measure flow. Water-based solutions work best with these types of meters, since the fluid must be conductive. For this meter to work, the liquid must fill the pipe with no voids. This type of meter does not obstruct the fluid’s flow as it’s measured, and it can be very accurate. However, this type of meter is ideal for continuous flow and generally won’t work well with intermittent stopping and starting.
Coriolis meters are mass flow meters. As the name implies, these meter use the Coriolis effect to measure the flow of liquid. This type of meter will compensate for changes in the liquid’s density. Coriolis meters are also very stable and accurate to as little as one tenth of a percent, so they’re ideal for precision liquid measurements.
With these considerations in mind, you can work with your equipment manufacturer more effectively and design liquid dosing systems that work best for your needs. Consider these components, as well as sensors and controls, as you design your liquid system.