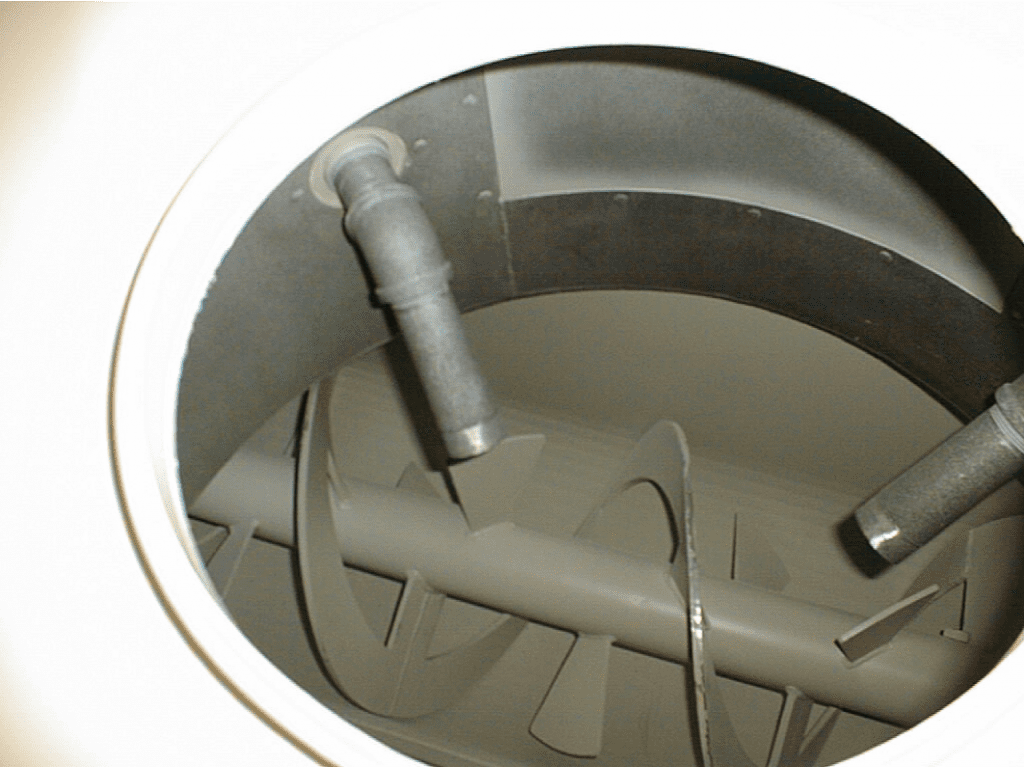
Screw conveyors are a simple, affordable and highly-effective material transportation method, when the conveyor is designed properly. The screw conveyor design can determine how quickly material moves through it, how the material is dispensed, and it can help to avoid problems, such as overworking the drive. Let’s take a closer look at screw conveyor design tips and tricks.
Screw Conveyors Design Basics to Optimize Your Conveyor
The basic design of a screw conveyor is simple, yet there are many ways to customize it. These screw conveyor design changes may appear to be subtle, however their impact on the overall functionality can be quite noticeable.
A basic screw conveyor uses a central shaft surrounded by screw flights. This mechanism is surrounded by an enclosure, which is open at either end to accept and dispense materials. Screw conveyors and screw feeders are similar in design, except screw conveyors are designed to transport material from one part of the process to the next, while screw feeders are designed to measure it as it flows.
Screw conveyor designs can be customized in many ways. The following are a few of the ways that manufacturers might customize a screw conveyor design to suit the needs of the application and materials. Note that this is not an exhaustive list; there are other ways to customize the screw conveyor to meet material handling needs.
- Pitch: the distance between the screw flights
- Shaft: the size of the central shaft, or the absence of it
- Construction: what the enclosure, shaft, flights, and other components are made of
- Capacity: how much material can move through the screw conveyor in a set time
- Speed: how quickly the screw conveyor moves
- Length: the total length of the conveyor
- Incline: whether the conveyor must cover vertical distance, and how much
Screw Conveyors and Materials Characteristics
The characteristics of the materials being conveyed impact the screw conveyor design significantly. There are many different materials characteristics that can impact the design, but the most important are included below:
- Flowability: Materials that flow very easily won’t require as much power to move, and will move faster. Materials that are more dense and sluggish will require more power, and will move slower.
- Corrosive: Corrosive materials will eat away at the screw, shaft and enclosure if they are not made from a resistant construction. Certain stainless steel grades or nickel alloys are ideal when working with corrosive materials.
- Abrasive: Abrasive materials will wear away at the screw, shaft and enclosure through friction. Abrasion resistant alloys will help to reinforce screw conveyors with these materials.
- Angle of Repose: The angle of repose will affect the material’s flow at varying inclines. If the screw conveyor is transporting materials across a vertical and horizontal distance, this will be particularly important.
- Special Characteristics: Many special characteristics can affect the screw conveyor’s operation and design, such as levels of moisture or oil, clumping, toxicity, stickiness, dustiness, flammability, explosiveness and more.
Flight Pitch, Number, Paddles and More
The pitch on the screw conveyor flights are an important consideration. At full pitch, the spacing between the flights is equal to the diameter of the feeder. At half pitch, the spacing between the flights is half of the diameter of the feeder. If the pitch across the flights is the same, pressure will build up towards the end of the conveyor. The pitch will also partially determine how much material moves through the feeder.
There are many ways to customize the screw conveyor pitch to adjust for the material characteristics, including the following:
- Progressive or Variable Pitch: A progressive or variable pitch is generally ideal for drawing materials out of a hopper evenly. In this case, the spaces between the flights increases to draw the material out of the hopper.
- Double flight: A double flight adds another spiral-shaped piece around the shaft to further increase the conveying power or amount. Double flight screw conveyors might also be progressive or variable pitch.
- Paddles: Adding paddles between screw flights can help to make a more gentle mixing and conveying action. This is especially helpful for brittle or friable materials or those prone to clumping.
- Ribbon flight: While a regular screw flight is solid all the way through, a ribbon flight has spaces between the flight and the shaft. This helps sticky or viscous materials move through the screw conveyor more easily.
Customizing your screw conveyor design can help to prevent material from getting stuck in the conveyor, prevent overworking the drive, and extend the useful lifetime of the conveyor. Carefully consider your materials, processes and facility layout, and work with an experienced manufacturer to design the ideal screw conveyor for your needs.